Manufacturers can use DPM to track parts throughout the manufacturing process and supply chain. It is ideal for locating parts for service or recall and can assist in liability and warranty resolution.
What is Direct Part Marking?
Direct Part Marking (DPM) is the process of marking manufactured parts with unique, permanent machine-readable codes containing key product information. These codes are applied by part marking machines. Component marking allows parts to be traced through the supply chain and each part’s lifecycle. Part identification also decreases the need for manual code entry, improves code accuracy and reliability, and speeds up data exchange.
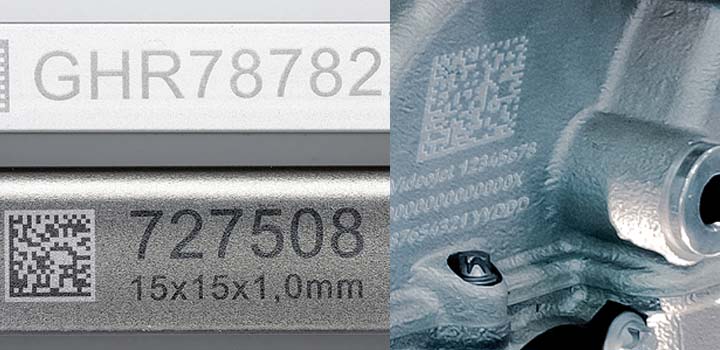
What is a DPM code?
Part numbers, serial numbers, batch codes and date codes are the most common types of DPM codes marked onto parts. But it can include other traceability information as well. These codes can be marked onto the part in the form of alphanumeric text, 2D Data Matrix codes, barcodes or symbols.
What are common methods of Direct Component Marking?
The most common direct part marking methods are Laser Marking, Continuous Inkjet Printing, Dot Peening and Electrochemical Etching.
Laser Marking uses CO2 or fiber lasers to apply the information directly onto the part by removing some of the substrate surface. Laser markers with different power outputs can be used to achieve different marking effects, from light etching to deeper engraving of the parts.
Continuous Inkjet Printing (CIJ) uses specialist inks to deliver robust, legible printing on nearly any surface, smooth or irregular. Inkjets can apply codes on the side, top, bottom or even the inside of a part. One key consideration with inkjet printing is making sure the part to be marked is clean so that the code will be clear.
Dot Peen Marking uses an indenting pin to create an indentation for each dot in the Data Matrix code. The contrast needed for accurate verification comes from the light that reflects differently on the indentations and the surface of the product.
Electrochemical Etching removes layers of material via electrolysis. This chemical etching process takes an image on a stencil and transfers it to an electrically conductive product by the action of electrolyte and electricity
What is Part traceability and why is it important?
Traceability is a process used to track a part throughout its lifecycle using a unique identification code. Traceability allows manufacturers to:
- Control the supply chain by keeping track of parts across the production process.
- Quickly locate parts for recall campaigns and service inquiries.
- Meet growing requirements and regulations.
- Protect against counterfeits.
Are there any changes in the industry?
The Aerospace, Automotive and Pharmaceutical industries are broadly all moving from one-dimensional (1D) towards two-dimensional (2D) coding – also known as Data Matrix codes. The advantages of 2D codes are:
- Contain more information in a small amount of space
- Can be applied with a variety of direct marking methods
- Have greater reading reliability
Which factors should a buyer consider when evaluating marking technologies?
- Substrate/Application (the surface being marked).
- Production Line (ease of integration and mobility).
- Budget (balancing upfront costs with lifetime upkeep).
Videojet Direct Part Marking Solutions
Videojet offers several technologies that meet a wide array of part marking applications. Learn more about:
Download the documents below to learn more
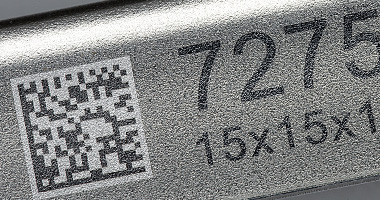
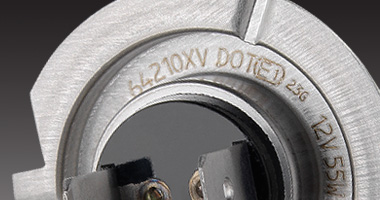
Categories
Contact Us
Equipment Sales:
01267 6687
Service & Support:
+353 1 267 6503 (Republic of Ireland)
03301233930 (Northern Ireland)